Introduction
Fly ash can be used as a cost-effective mineral filler in hot mix asphalt (HMA) paving applications. Where available locally, fly ash may cost less than other mineral fillers. Also, due to the lower specific gravity of fly ash, similar performance is obtained using less material by weight, further reducing the material cost of HMA. Mineral fillers increase the stiffness of the asphalt mortar matrix, improving the rutting resistance of pavements. Mineral fillers also help reduce the amount of asphalt drain down in the mix during construction, which improves durability of the mix by maintaining the amount of asphalt initially used in the mix.
Fly ash will normally meet mineral filler specification requirements for gradation, organic impurities and plasticity. Also, fly ash is hydrophobic (non-water wettable) , reducing the potential for asphalt stripping; the presence of lime in some fly ashes may alsoreduce stripping. Mineral fillers have become more necessary as mixture gradations have become coarser. Asphalt pavements with coarse gradations are increasingly being designed because they perform well under heavy traffic conditions. Some mixtures require higher dust to asphalt ratios than can be gained through the recycling of baghouse fines alone.
Mix Design and Specification Requirements
Fly ash must be in a dry form when used as mineral filler. Typically, fly ash is handled in a similar manner to hydrated lime – it is transported to the HMA plant in pneumatic tankers; stored in watertight silos at the plant; and metered into the HMA using an auger.
Engineering Properties. The physical requirements for mineral filler in bituminous paving are defined in AASHTO M 17, Table 8-1.
Organic impurities. Although no standard for carbon content or LOI is specified for fly ash used as mineral filler, laboratory asphalt mortar evaluations incorporating fly ashes with LOIs up to 10 percent perform satisfactorily.
Plasticity. Fly ash is a non-plastic material.
Figure 8-1: Stone matrix asphalt.
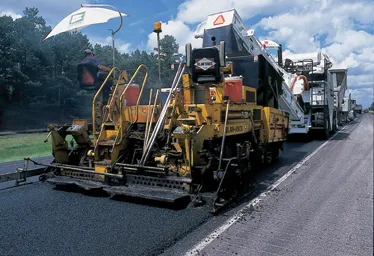
Table 8-1: AASHTO M 17 specification requirements for mineral filler use in asphalt paving mixtures. | |||
Particle Sizing | Organic Impurities | Plasticity Index | |
Sieve Size | Percent Passing | ||
600mm (No. 30) | 100 | Mineral filler must be free from any organic impurities | Mineral filler must have plasticity index not greater than 4 |
300mm (No. 50) | 95 – 100 | ||
75mm (No. 200) | 70 – 100 |
Gradation. Most fly ashes typically fall within a size range of 60 to 90 percent passing the 75 ยตm (No. 200 sieve).
Fineness. There is no fineness standard for mineral filler beyond the AASHTO M 17 gradation requirements; however, when Stone Matrix Asphalt (SMA) was first introduced to the U.S. in 1990, often a requirement for a maximum percent passing the 20 ยตm (No. 635) sieve was specified. Typically, fly ash has 40 to 70 percent passing the 20 ยตm sieve and performs well in mortar testing and field performance.
Specific gravity. The specific gravity of fly ash varies from source to source; it is typically 2.0 to 2.6. Most “non-fly ash” mineral fillers have a specific gravity ranging from 2.6 to 2.8; therefore, HMA designed with fly ash will usually require a lower percentage by weight to obtain the same performance (e.g., voids in mineral aggregate, stiffness, drain down, etc.).
Rigden voids. Research indicates that mineral fillers with more than 50 percent voids as determined using the modified Rigden’s voids test tend to overly stiffen the asphalt binder. Most fly ashes have a Rigden void of less than 50 percent.