Fly ash grouts are used for sealing voids beneath pavement slab sections. The unconfined compressive strength requirements for a grout mixture will usually exceed 8,300 kPa (1,200 psi) at 28 days and will range between 4,100 and 5,500 kPa (600 and 800 psi) at 7 days. This strength profile for grouts differentiates them from flowable fill materials inasmuch as the flowable fill definition (or controlled low strength material) sets an unconfined compressive strength limit of 8,300 kPa (1,200 psi) at 28 days. Furthermore, the relatively small size of the void filled with the grout mixture further differentiates this application from the larger voids where the lower strength flowable fills are utilized.
The principal requirements for a slab stabilization material is that it can flow to fill very small voids and still have adequate strength to support the slab. A good stabilization material should remain insoluble, incompressible, and not erode after it has been placed and hardened. It should also have sufficiently low internal friction to flow into very small voids and water channels. If the material is too stiff, it will create a seat below the grout hole and not fill all voids. If it is too wet, it will not have enough strength to support the slab and may have a large amount of shrinkage. Finally, it should have sufficient body to displace free water from under the slab and develop adequate strength and durability.
Figure 9-1: Fly ash grouts for pavement subsealing.
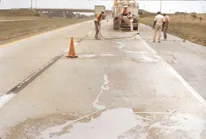
Mix Design and Specification Requirements
Mix design. A typical cement-fly ash (Class F) mix design calls for 1 part cement (Type I, II, or III), 3 parts fly ash, and enough water for flowability, usually about 1.5 to 3.0 parts water. It may be possible to reduce the cement component if a Class C ash is used. Water content is determined using a flow cone and ASTM C 939. The flow cone measures the flowability of the grout mixture. The time of efflux is the flow time in seconds required to empty the cone. A time of efflux in the range of 10 to 16 seconds gives the best flowability and strengthens cement-fly ash grout slurries. The determination of initial set time of the grout in laboratory tests is useful in comparing various mixes. Usually, the Proctor Needle Test (AASHTO T 197/ASTM C 403) is used. Typical set times with these tests are 1½ to 2 hours.
Additives. It may be necessary to use additives or admixtures in fly ash-cement grouts to achieve the required goals of flow, set time, shrinkage and strength.
Types of additives may include accelerators such as calcium chloride to reduce set times; retarders to increase set time; expanding materials such as powdered aluminum to offset shrinkage; friction reducers or pumping aids to ease pumping, increase flow, and aid in cleanup; wetting and dispersing agents to get a more uniform mixture; and water-reducing agents to lower the water content.
Strength. A minimum strength requirement is normally used to ensure the durability of the grout. A typical value is 4,100 kPa (600 psi) at 7 days measured by the standard mortar cube test, AASHTO T 106 (ASTM C 109). A pozzolan-cement grout is typically designed to achieve a 7-day compressive strength of 4,100 to 5,500 kPa (600 to 800 psi). The ultimate strength of the grout will be much higher (10 to 28 mPa/1,500 to 4,000 psi).
Construction Practices
Equipment. In the past, most grouting/stabilization contractors used batch mixers and bagged materials. Today’s contractors use very mobile, self-contained units that carry all the equipment and materials needed for slab stabilization. The dry materials are packaged in either uniform-volume bags or measured by bulk weight.
A colloidal mixer is needed to produce the cement-fly ash grouts. Grout mixes made by these mixers stay in suspension and resist dilution by free water. The two most common types of colloidal mixers are the centrifugal pump and the shear blade. The first pulls the grout through a high-pressure centrifugal pump at high velocity. The shear blade slices through the grout at speeds between 800 rpm and 2000 rpm. The high shearing action and subsequent pressure release of these mixers de-aerate the solid particles, which allows them to be wetted to make a more homogeneous mixture. It is not recommended to use paddle-type drum mixers to produce cement-fly ash grouts. Grout should never be mixed using a screw conveyor, a mortar mixer, or a ready mix truck. Mixes made with these devices will not be homogenous and will require more water to promote flowability.
Injection holes. Grout injection holes are drilled in a pattern determined by the contracting agency in consultation with the contractor. They are typically no larger than 50 mm (2 in) in diameter, drilled vertically and to a depth sufficient to penetrate any stabilized base and into the subgrade material to a depth of no more than 76 mm (3 in). The holes can be washed with water or blown with air to create a small cavity to better intercept the voids beneath the pavement.
Upon completion of the subsealing, all drilled holes are sealed flush with the pavement surface with a fast-setting concrete or other patching material approved by the engineer.
Pumping and vertical grade control. String lines are established above the pavement to monitor movement during subsealing. An expanding rubber packer or other approved device is lowered into the drilled holes. The discharge end of the packer or hose must not extend below the lower surface of the concrete pavement.
The pressure in the grout must be monitored by an accurate pressure gauge in the grout line that is protected from the grout slurry. Continuous grout pressures to 1,400 kPa (200 psi) are typical, with pressures to 2,100 kPa (300 psi) allowed only for short periods. In the event the pavement is bonded to the subbase, brief pressure rises (10 seconds or fewer) to 4,100 kPa (600 psi) are not unusual. Allow the water displaced from pavement system voids by the grout to flow freely. Take appropriate measures to prevent excessive loss of the grout through cracks and joints or in the shoulder area.
Opening to traffic. The time allowed before traffic can get back on the grouted slabs varies considerably. Deflection measurements taken after slab stabilization have shown that the deflections are reduced over a period of 30 minutes to 3 hours. Grout hardening depends on the temperature, degree of confinement, and grout properties.
Cautions
Pavement movements above the specified tolerances may require grinding or even removal and replacement of the pavement. Existing cracks in the pavement should be marked prior to subsealing operations. New cracks radiating diagonally through the grout injection holes typically will be presumed to have been caused by improper injection techniques and could result in penalties to the contractor or even removal and replacement of the pavement.
When the ambient air temperature is between 2 degrees C and 10 degrees C (35 degrees F and 50 degrees F), add an accelerator to the grout mix. When calcium chloride is used, it must be thoroughly pre-mixed with the water before the addition of dry ingredients. Cement-fly ash grouts should not be used when the ambient temperature is below 2 degrees C (35 degrees F) or when the subgrade is frozen.
Comments are closed