Determining the cause of structural failures is the challenging discipline of forensic structural engineering. Determination of civil and criminal liabilities drive many such investigations, but there are also valuable lessons to be learned from these failures.
Not So Elementary, My Dear Watson
Collecting facts to recreate the scene of a crime has been a fascinating fictional story plot long before Sherlock Holmes became popular. In reality, the investigating detective may not work in law enforcement but instead, work in the extremely interesting field of forensic engineering. And the case may not necessarily involve criminal activities although many such cases arise. Instead the investigator may simply be determining the cause of failure in order to improve materials, designs, and intended use of an engineered product or structure.
One of the first applications of structural failure analysis may have been developed by the early engineers of the Roman Empire. As the story goes, engineers who built arches were expected to stand beneath the completed construction as the supporting formwork was removed. If the structure held together properly, the engineer lived to begin the next project. If the structure collapsed, the surviving engineers and apprentices presumably gained valuable insight on how bad design, materials, workmanship, and/or overloading affect structural performance.
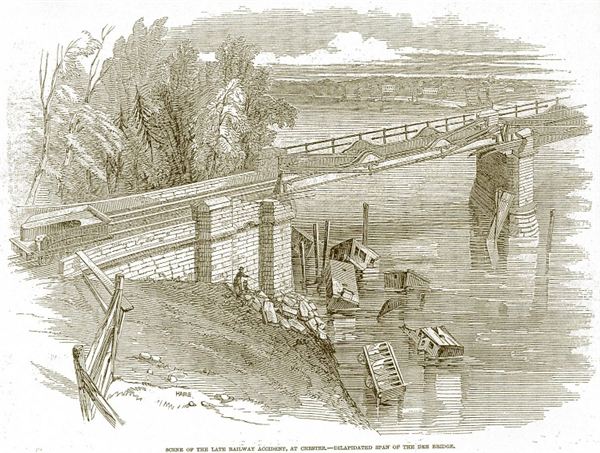
160 Years Ago
A more recent, and possibly the first, well-documented example of complete structural failure analysis resulted from the 1847 collapse of the Dee River railroad bridge in England. It was built using cast iron main girders between spans with wrought iron supports. After extra ballast had been applied to the track across the bridge as a precautionary measure against timber fires, one of the spans collapsed under a passing train causing injuries and fatalities.
The incident initiated a review process which is generally followed by forensic engineers to this day: an investigation was performed by a lead engineer who examined the site of the failure, collected materials, performed testing and analyses, reviewed witness statements, recreated events, and formulated a report attributing causation of the structural failure. And like modern investigations today, the failure analysis was not conclusive, but was able to determine probable cause. The design was deemed defective allowing fatigue failure of a cast iron beam, exacerbated from the weight of the extra ballast which had been applied only a few hours prior to the collapse. The wrought iron supports did not strengthen the structure as intended due their poor design implementation in the structure. Testing of the materials showed cast and wrought iron was prone to fatigue cracking failure, calling into question its use on other bridges and structures. Finally, continued failure of bridges and other structures using cast and wrought iron led to the development of high strength steels and other alternative materials.
A Few Years Ago – Lesson Learned?
Forensic engineering has come a long way since those early days. Professional associations, advanced degrees, certifications, and consulting services abound. Vaster understanding of material properties and usage has led to better engineering design. Dedicated laboratories and computer simulations have become highly developed tools to analyze material and system failures. Tragically, however, forensic engineering is still required for failures involving loss of life and limb.
Expert witness testimony is commonplace to determine criminal and civil liabilities. Strategically placed cameras and data recording systems can often capture failures as they occur, greatly reducing the uncertainty of conflicting eyewitness reports. And bridges still fall due to failed material and poor design, as the all too recent collapse of the I-35W overpass in Minnesota confirmed over 160 years after the Dee River bridge failure. Incredible as it may seem, the resulting 2008 NTSB report attributes the collapse to inappropriate addition of covering material dead load, in this case 2″ of concrete overlays, and failed design of supporting members, in this case undersized gusset plates.