Spray-on fireproof coatings are an effective method for protecting equipment and structures from fire and heat. However, these materials tend to have particular advantages and disadvantages. Read this article to learn about the properties, indications and applications for these coatings.
An intumescent paint is a type of coating that is a fire retardant that also protects structural members from the ill effects of hot weather and sun exposure. It can be applied to wood, bricks, walls, and other structural members of a structure, to steel and plastic piping, and to fiberglass structures. These coatings are usually made of organic substances like epoxy resins and other thermosetting polymers that have high resistance to heat and fire.
How Intumescent Spray-On Fireproofing Works
Intumescent substances swell when exposed to heat and fire. When used as a paint coat or fireproofing spray, they form a protective layer on the surface. When exposed to fire or excessive heat, the protective layer will resist and absorb heat, thus protecting the structural member from damaged or deformation. Volume expansion and density reduction takes place when temperature starts to rise. Organic materials used for the manufacturing of intumescent paints are inert at low temperatures, but they swell instantaneously when brought into contact with heat or fire.
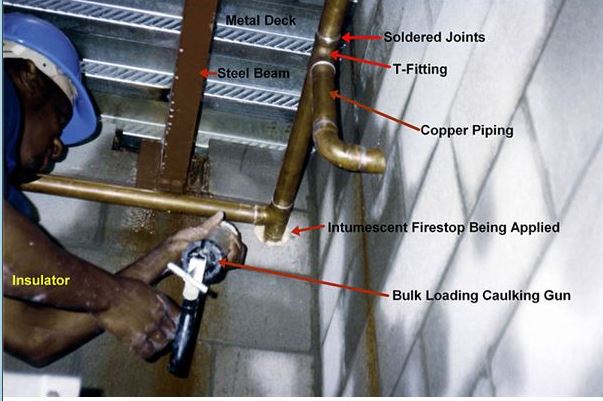
Intumescent paints are either solvent based or water based. In both cases, they contain a sufficient amount of hydrates to help in cooling off the temperature because of evaporation effects. Water based paints are used most often because they are inexpensive and widely available. Solvent based intumescent paints have, so far, seen only limited usage.
Another classification system, which takes into account the nature of the char produced by intumescent paint, is also in effect.
Soft char intumescent paints produce only a light char upon initial heat exposure. The char is a bad conductor of heat, and it does not allow the heat to pass through the paint coat and reach the structural member. It also contains hydrates which have a cooling effect. This is used primarily for the protection of structural steel.
Hard char intumescent paints produce hard char, which is also a very poor conductor of heat. These paints are exclusively used for plastic pipe protection. The major constituents of hard char are graphite and sodium silicate.
Advantages and Applications
Intumescent coatings prolong the structural life of steel. As protected steel is less exposed to frequent temperature variations, its load bearing capacity also increases.
The coatings can be applied off-site as well as on-location. Off-site fireproofing means there is enough time for workers to fit, erect, and adjust their structural components. Faster and easier construction, reduced on-site activities, and ease of assembly are the major advantages of off-site coating.
These specialized paints have a wide range of use. They can be used for steel coatings, wooden coats, or for structural components like concrete as well. Recently intumescent fireproofing sprays have been developed that can be applied to fiber glass structural components, too.
Advantageous use of these products can be made in refurbishment projects. The structural, aesthetic, and architectural value of the structural objects remains preserved.
As already stated, intumescent paints have a huge scope of use. These paints are mainly used in fire-stopping, closures, and fireproofing works in buildings, houses, and manufacturing industries. Gasketing applications also make use of intumescent spray-on fireproofing paints. Major use of these paints is found in offshore drilling, aircraft maintenance, and the ship building industries.
Disadvantages
The intumescent fireproofing industry is on the rise and has already created a stir in the market. However, there are certain drawbacks associated with these paints.
UV exposure, operational heat, and the humidity of the work area are three major factors that affect the performance of intumescents. Intumescents are particularly vulnerable to environmental exposure at the time of application.
For sodium silicate based intumescent fire sprays, having rubber or epoxy in the coatings becomes mandatory in order to promote adherence.
They have a limited fire resistance period. The best quality, i.e. most expensive, intumescent fire sprays will not preserve your structural member for more than sixty minutes or so. As the fire resistance time duration increases, the costs also increases, and the cost rise is usually exponential.
Alternatives to the Intumescent spray-on paints are also available in the market.
Flexible blanket systems – Good – cheap, easy to use, dry fixing methods; bad – poor appearance.
Other fireproofing sprays – Good – covers complex details, low cost, durable; bad – on site application means more on-site headaches.
Board systems – Good – clean appearance, dry fixing, can be used on unpainted steelwork; bad – does not cover complex areas.
Comments are closed