A large quantity of iron and steel is damaged because of corrosion, causing huge losses that may have been minimized by the adoption of appropriate preventive measures. Corrosion products from oxidation do not adhere to the metal surface, and the resultant pitting deteriorates the structure.
What Is Corrosion
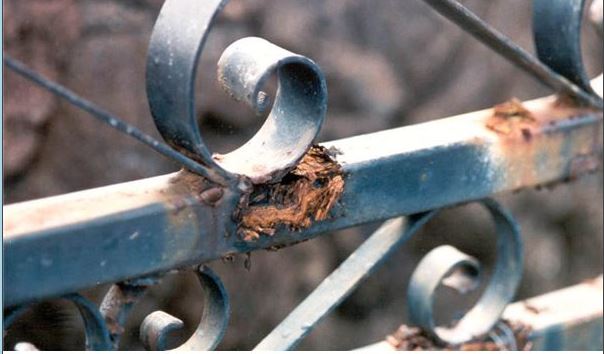
Corrosion is a natural event that causes the weakening ofa material, usually a metal, or its characteristics due to reactions with the environment.
Some environments are more suitable for the chemical combination of metals with elements to create compounds and come back to their low energy levels.
Corrosion is a serious condition of the substance that may produce massive damage to the product, including bridges, buildings, water systems, and home appliances, unless suitable prevention and control techniques are applied.
The Chemical Reaction In Corrosion
A substance disintegrates into atoms because of the chemical reactions with the water and oxygen in the environment, resulting into an electron loss of the material.
If an electrical circuit is completed, the metal atoms become positively charged ions, causing pitting or the development of a crack.
The rate of pitting corrosion is greater in portions where welding operations have caused micro structural transformations. Localized corrosion may initiate fatigue that can intensify by the action with corrosive agents like seawater.
In an electrochemical corrosion, the strength of iron is reduced due to the oxidation of its atoms that is called rusting, by which oxides are formed.
Rusting Of Iron
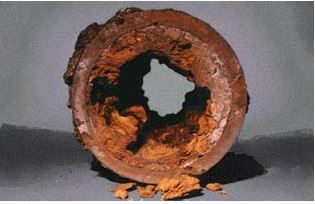
The most significant category of corrosionis the rusting of iron, which produces iron oxides due to the reaction of iron with oxygen in an environment of humid air or water.
Metal corrosion will also occur by a chemical reaction with gaseous substances like acid vapors, ammonia gas, and gases containing sulpher.
Corrosion particularly signifies the process that is related to the weakening or degradation of the metal parts, and the processes are generally electrochemical in nature. Rust formed is brittle and prominent as a reddish crust on the exposed fresh iron surface.
Formation of rust can be minimized by the exclusion of the air and water from the surface of the iron by the application of paint, oil, grease, or a shielding coat of another metal such as chromium, zinc, or nickel. Stainless steels do not corrode because of the addition of protective coatings of nickel or chromium that form a rigid coating to withstand additional attack.
Rust Prevention By Galvanization
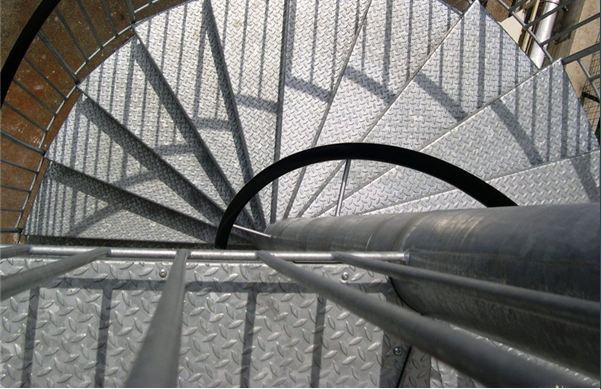
Rust prevention is important to avoid damage to expensive equipment and appliances. Several techniques are being employed for this purpose.
Galvanization is a metallurgical process in which a zinc coating is applied on steel or iron to avoid rust, since the corrosion resistance of zinc is superior to those of steel and iron.
Coatings of zinc achieve corrosion prevention of the protected metal by the formation of a physical obstruction, and by functioning as an anode if this obstruction is destroyed.
On exposure of zinc to the atmosphere, zinc oxide is formed by the reaction of zinc with oxygen that further reacts with molecules of water in the air to form zinc hydroxide.
Reaction of zinc hydroxide with carbon dioxide in the atmosphere creates a thin and insoluble layer of zinc carbonate that prevents further corrosion. Preservation of iron and steel by the process of galvanization is preferred because it is economical and simple in application.
What is Electroplating
Electroplating is another method through which iron or steel can be protected and prevented from rusting and corroding. Here, the metal to be protected is coated by a thin layer of another metal having non-rusting properties by reducing it.
Normally, the metals involved form the electrodes, which are processed inside an electrolyte by passing electric current (DC) across the electrodes, through the electrolyte.
In this process the electrode which is connected to the negative of the supply gradually gets covered with the metal of the electrode connected to the positive of the electric supply which slowly disintegrates or reduces and becomes attached over the other electrode.
The electrode connected to the negative is the one which is being electroplated for the required protections.
The above process can be explained and witnessed through a small experiment.
You will need the following materials for the experiment:
One iron nail
One copper rod
Water
Copper sulphate crystals
A 9 Volt Battery
Procedure:
Take a vessel and fill it with water, add a teaspoon full of copper sulphate crystals in the water and mix it thoroughly.
Copper sulphate not only helps to enhance electricity conduction through water, but also directly participates in the process by extracting copper from the copper rod and attaching it over the exterior of the nail.
Arrange the nail and the copper rod such that some part of them are immersed in the solution and are placed rigidly and vertically, as shown in the diagram.
Make sure that the metals do not touch each other.
Obviously, here the iron nail is the component we want to electroplate or cover with some kind of layer. So the nail has to become the cathode terminal and the copper rod can be selected as the anode terminal.
Connect them appropriately to the battery poles, as explained above.
The electroplating process will be instantly initiated and after a few hours you should be able to find the dipped portion nail completely covered with copper deposits, received from the copper rod which in the course can be seen to have become much thinner (eroded) over the immersed area.
Electroplating, an Experiment
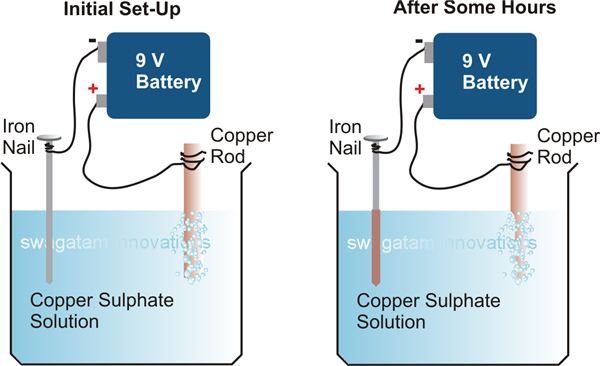
Comments are closed