In the future, automobile makers will be required to produce new technologies that reduce automotive emissions while still satisfying the ever increasing performance demand of drivers. Active safety control systems such as Anti-lock Brake System (ABS), Electronic Braking force Distribution (EBD), Traction Control System (TCS) and Electronic Stability Program (ESP) need to improve their existing braking functions in order to be truly effective in improving driving safety. Therefore, brake systems will need to be faster and more sophisticated when controlling braking forces at the wheels. In addition, smaller pedal pressure and reduced stroke will be required to produce a larger braking force. With ABSs, the surge and fluctuation of pedal force gives the driver an uncomfortable feeling. These are only a few of the problems and technical limitations of current braking control systems (Semm et al., 2003, Peng et al., 2008).
Figure 1 shows the development trend of braking control systems. The future development in braking technology will progress towards brake-by-wire; therefore, brake manufacturers will need to take a greater interest in the development of Electro-Mechanical Brake (EMB) systems (Line et al., 2004, Emereole & Good, 2005)
EMB systems replace conventional hydraulic braking systems by eliminating the hydraulics and replacing them with electrical components. They are able to eliminate the large vacuum booster found in conventional systems, which helps to simplify production of right- and left-hand drive vehicle variants. When compared to conventional braking systems, EMB systems offer increased flexibility for components placement by totally eliminating the hydraulic system (Nakamura et al., 2002). Figure 2 shows the comparison of EMB and EHB (Electro-Hydraulic Brake) systems.
This paper investigates the modeling and simulation of EMB systems for Hybrid Electric Vehicles (HEV). The HEV powertrain was modeled to include the internal combustion engine, electric motor, battery, and transmission. The performance simulation for the regenerative braking system of the HEV was performed using MATLAB/Simulink. The control performance of the EMB system was evaluated via simulation of the regenerative braking of the HEV during various driving conditions.
Source: Urban Transport and Hybrid Vehicles, Book edited by: Seref Soylu,
ISBN 978-953-307-100-8, pp. 192, September 2010, Sciyo, Croatia, downloaded from SCIYO.COM
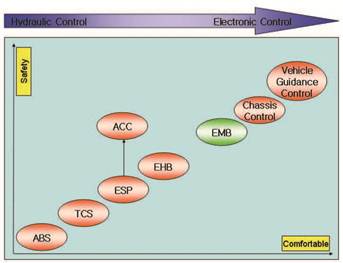
Fig. 1. Development trend of brake control systems
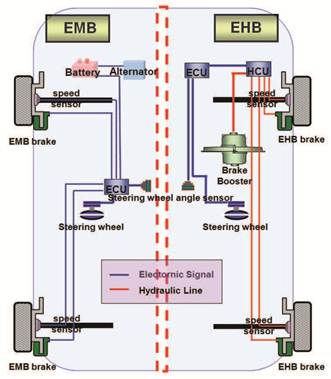
Fig. 2. Comparison of EMB and EHB systems
HEV powertrain modeling
Figure 3 shows the structure of the HEV investigated in this paper. The power source of this HEV is a 1.4 liter internal combustion engine and a 24 kW electric motor connected to one of the axes. The transmission and braking system are an Automated Manual Transmission (AMT) and an EMB system with pedal stroke simulator, respectively. EMB supplies braking torque to all four wheels independently, and the pedal stroke simulator mimics the feeling of the brake pedal on the driver’s foot.
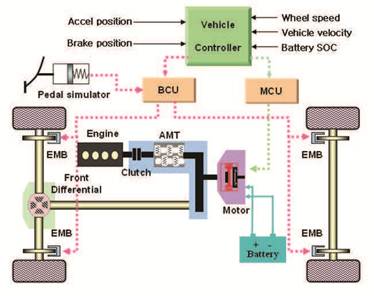
Fig. 3. Configuration of HEV braking control system
The vehicle controller determines the regenerative braking torque and the EMB torque according to various driving conditions such as driver input, vehicle velocity, battery State of Charge (SOC), and motor characteristics. The Motor Control Unit (MCU) controls the regenerative braking torque through command signals from the vehicle controller. The Brake Control Unit (BCU) receives input from the driver via an electronic pedal and stroke simulator, then transmits the braking command signals to each EMB. This is determined by the regenerative braking control algorithm from the value of remaining braking torque minus the regenerative braking torque. The braking friction torque is generated when the EMB in each wheel creates a suitable braking torque for the motor; the torque is then transmitted through the gear mechanism to the caliper (Ahn et al., 2009).
Engine
Figure 4 shows the engine characteristic map used in this paper. The complicated characteristics of this engine are due to many factors, such as fuel injection time, ignition time, and combustion process. This study uses an approximated model along with the steady state characteristic curve shown in Figure 4.
The dynamics of the engine can be expressed in the following equation:

where Je is the rotational inertia, ωe is the engine rpm, Te is the engine torque, Tloss is loss in engine torque, and Tclutch is the clutch torque.
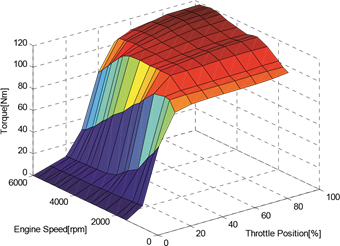
Fig. 4. Engine characteristic map
Motor
Figure 5 shows the characteristic curve of the 24 kW BLDC motor used in this study. In driving mode, the motor is used as an actuator; however, in the regenerative braking mode, it functions as a generator.
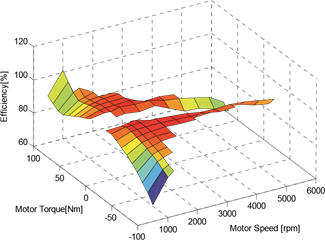
Fig. 5. Characteristic map of the motor
When the motor is functioning as an actuator, the torque can be approximated using the following 1st order equation:

where Tm is the motor torque, Tm_desired is the required torque, and τTm is the time constant for the motor.
Battery
The battery should take into account the relationship between the State Of Charge (SOC) and its charging characteristics. In this paper, the input/output power and SOC of the battery are calculated using the internal resistance model of the battery. The internal resistance is obtained through experiments on the SOC of the battery. The following equations describe the battery’s SOC at discharge and charge.
• At discharge:

• | At charge: ![]() |
where SOCdis is the electric discharge quantity at discharge mode, SOCchg is the charge quantity of the battery, Qm is the battery capacity, and ηA(ia ,τ) is the battery’s efficiency.
Automated Manual Transmission
The AMT was modeled to change the gear ratio and rotational inertia that correspond to the transmission’s gear position. Table 1 shows the gear ratio and reflected rotational inertia that was used in the developed HEV simulator.
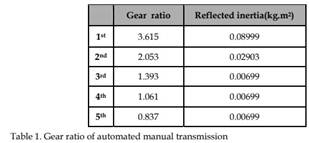
The output torque relationships with respect to driving mode are described in Table 2. At Zero Emission Vehicle (ZEV) mode, the electric motor is only actuated when traveling below a critical vehicle speed. In acceleration mode, the power ratio of the motor and the engine is selected in order to meet the demands of the vehicle. At deceleration mode, the regenerative braking torque is produced from the electric motor. The above stated control logic is applied only after considering the SOC of the battery.
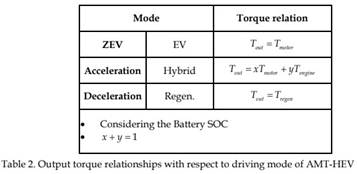
Vehicle model
When the engine and the electric motor are operating simultaneously, the vehicle state equation is as follows (Yeo et al., 2002)
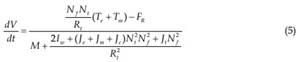
where V is the vehicle velocity, Nf is the final differential gear ratio, Nt is the transmission gear ratio, Rt is the radus of the tire, FR is the resistance force, M is the vehicle mass, Iw is the equivalent wheel inertia, and Je, Jm, Jc, and Jt are the inertias of engine, motor, clutch, and transmission, respectively.
EMB system
The EMB system is environmentally friendly because it does not use a hydraulic system, but rather a ‘dry’ type Brake–by-wire (BBW) system, which employs an EMB Module (i.e., electric caliper, electro-mechanical disk brake) as the braking module for each wheel. The EMB system is able to provide a large braking force using only a small brake pedal reaction force and a short pedal stroke.
Structure of EMB system
Motors and solenoids can be considered as the electric actuators for EMB systems. The motor is usually chosen as an actuator of the EMB system because the solenoid produces such a small force corresponding to the current input and has such a narrow linear control range that it is unsuitable. In order to generate the proper braking force, Brushless DC (BLDC) and induction motors are used due to their excellent output efficiency and remarkable durability, respectively. Figure 6 shows a schematic diagram of an EMB system.
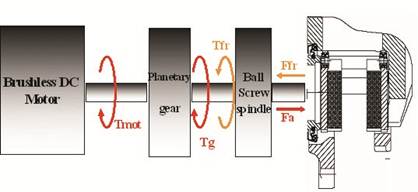
Fig. 6. Schematic diagram of the EMB system
Friction forces are the result of changing resistance of the motor coil and the rigidity of the reduction gear due to temperature fluctuations. To compensate for friction, the control structure for EMB torque adopts a cascade loop. The loop has a low level control logic consisting of the current and velocity control loop shown in Figure 7. This structure requires particularly expensive sensors to measure the clamping force and braking torque; therefore, this paper uses a technique that estimates their values by sensing the voltage, current and position of the DC motor based on the dynamic model of the EMB (Schwarz et al., 1999).
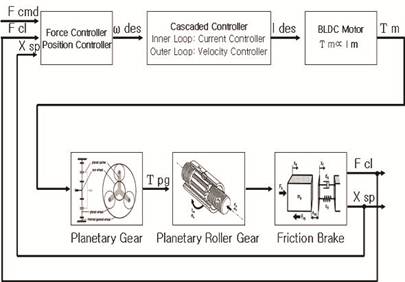
Fig. 7. Control structure of EMB system
Simulation model of EMB system
Figure 8 shows the EMB performance analysis simulator developed in this paper. Force, speed, and electric motor current are fed back via the cascaded loops and controlled by the PID controller.
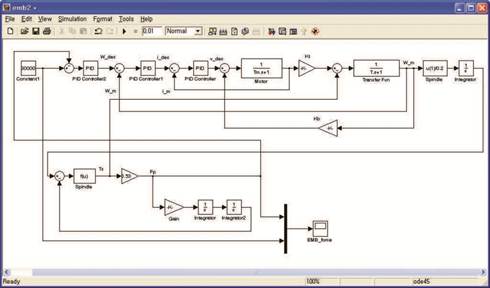
Fig. 8. EMB simulation model
Figure 9 shows the response characteristics of the EMB system. The step response in the time domain is shown at a brake force command of 14 kN.
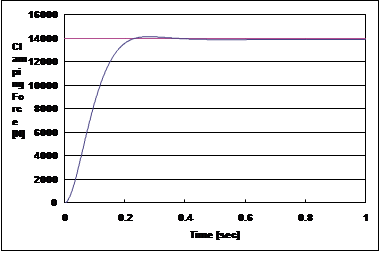
Fig. 9. EMB step response to a force command of 14 kN
Regenerative braking control algorithm
In conventional vehicles, the energy required to reduce velocity would normally be dissipated and wasted as heat during braking. On the other hand, HEVs have a regenerative braking system that can improve fuel economy. In an HEV, the braking torque is stored in a battery and regenerated through the electric motor/generator (Yaegashi et al., 1998). In this paper, the regenerative braking torque and EMB torque were determined according to the demand of the driver, the characteristics of the electric motor, the SOC of the battery, and the vehicle’s velocity. When the regenerative braking power is bigger than the driver’s intended braking power, the brake system generates only the regenerative braking torque. When this occurs, the BCU should control the magnitude of regenerative braking torque from the regenerative electric power of motor/generator in order to maintain a brake feeling similar to that of a conventional vehicle (Gao et al., 1999). In this paper, the control algorithm for maximizing regenerative braking torque is performed in order to increase the quantity of battery charge.
Decision logic of regenerative braking torque
Figure 10 shows the flow chart of the control logic for regenerative braking torque.
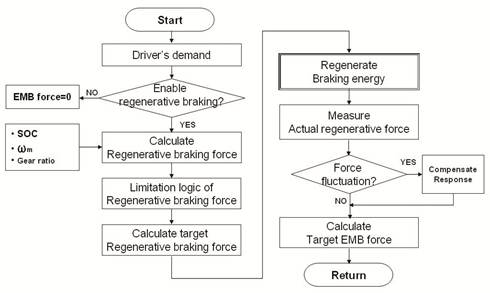
Fig. 10. Regenerative braking control logic flow chart
First, sensing the driver’s demand for braking, it calculates the required brake force of the front and rear wheels by using the brake force curve distribution. Then, the logic decides whether the braking system should perform regenerative braking, depending on the states of the accelerator, the brake, the clutch, and the velocity of both engine and vehicle, and on the fail signal. If regenerative braking is available, the optimal force of regenerative braking will subsequently be determined according to the battery’s SOC and the speed of the motor. Finally, the algorithm will calculate the target regenerative braking torque. In a situation where the fluctuation of the regenerative braking causes a difference of torque, the response time delay compensation control of the front wheel could be used to minimize the fluctuation of the target brake force. After the target braking torque is determined, the remainder of the difference between target braking torque and the regenerative braking torque will be transmitted via the EMB system.
Limitation logic of regenerative braking torque
Overcharging the battery during regenerative braking reduces battery durability. Therefore, when the SOC of the battery is in the range of 50%-70%, the logic applies the greatest regenerative torque; however, when the SOC is above 80%, it does not perform regeneration (Yeo et al., 2004).
HEV performance simulator using MATLAB/Simulink
The brake performance simulator was created for validating the regenerative braking control logic of the parallel HEV. The modeling of the HEV powertrain (including the engine, the motor, the battery, the automated manual transmission, and EMB) was performed, and the control algorithm for regenerative braking was developed using MATLAB/Simulink. Figure 11 illustrates the AMT-HEV simulator.
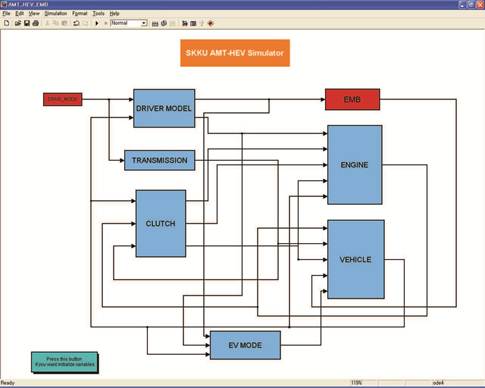
Fig. 11. AMT-HEV simulator with EMB
Simulation results
The simulation results for the Federal Urban Drive Schedule (FUDS) mode using the performance simulator are shown in Figure 12.
According to Figure 12, the brake pedal and accelerator positions are changing relative to the drive mode. Subsequently, the vehicle’s velocity successfully chases the drive mode. The torque of the engine and the motor is illustrated in the figure. The graph of battery SOC adequately shows charging state by regenerative braking during deceleration.