Rumble strips whether used on edges or centerline of roads are considered a road safety feature as the vibration and rumbling that they produce help to alert drivers who are inattentive.
Rumble Strips as Safety Devices
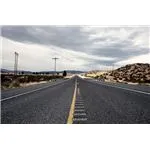
Rumble strips and centerline rumble strips are being used to reduce accidents and warn inattentive drivers. Rumble strips can even be laid across a travel lane so that they can warn drivers that they are approaching areas ahead where they need to exercise caution. Such strips are also accompanied by signage warning of the impending danger. Rumble strips were first used in 1952 and have followed a number of designs. Initially the asphalt pavement was itself milled or formed in such a way as to create the indentations required for the rumble strips. This has now been totally replaced by ceramic or plastic raised systems made famous by Botts’ Dots. Such strips produce rumbling that creates specific frequencies in the audible range and traffic engineers have used this to create singing shoulders or musical roads.
Image Source: Flickr – mikew
Rumble strips have however not been without their share of controversy, and people staying near freeways have complained against the noise produced by such rumbling strips. As a result many authorities do not install rumble strips in suburban areas where low speed restrictions are in place. Rumble strips are also sometimes viewed as a hazard for cyclists, whose narrow wheel base may find the rumble strips difficult to ride over. Climate is another factor that does contribute to the success or failure of a rumble strip. In northern areas prone to severe winters, such strips can get filled with ice or even traction sand and become ineffective. This can also happen in desert or sandy areas where winds can fill up the space in the rumble strips. Steering wheel vibration is another aspect that worries traffic engineers, and this has something to do with the gaps between rumble strips and is being studied for the best pattern to be followed.
The Importance of Centerline Rumble Strips
Centerline rumble strips are mainly used on two lanes, two way roadways and are meant to create warnings for drivers to avoid potential accidents with opposing traffic. Accidents happen due to side swiping or head on collisions. It has been established that the installation of centerline rumble strips has led to reduction in such accidents, especially on rural roads, most of which fall into the two lanes, two way roads category. Such roads do not have any dividing medians and thus no impending mechanisms to traffic running in opposite directions.
Different designs of the centerline rumble strips have led to the use of double 4 inch strips laid parallel to the road and 6 inch lateral strips that are said to increase visibility as well as prevent damage to the center line strips. Other designs use strips that may be laid continuously or in lengths of 12 inch to 30 inch with the width varying from 4 to 8 inches. Depth of grooves is normally kept at half an inch, which is considered enough to produce the rumble. Centerline rumble strips require very little maintenance and do not contribute to degradation of the pavement as had been the apprehension.
Making Centerline Rumble Strips
Centerline rumble strips can be milled on the center of the roadway with machines that have been specially designed for this job. Quite often painted lines are also used in addition to the rumble strips for better visual identification. These lines can be on both sides of the milled rumble indentation. In such cases the width of the rumble strip is reduced. Spacing between strips can be 12 to 24 inches, though the maximum decibels which serve as warning are in those strips that have a 12 inch distance. Length of strips in the direction of traffic is best at 6 inches and the width across traffic 12 inches. A depth of about a quarter of an inch in the milled surface is considered adequate to produce the sound caused by air being forced out of the depression. Carpeting or relaying of the surface of a road would require that these rumble strips have to be redone. It has to be however ensured that the thickness of the new layer is sufficient to take the new milling that is required to create the rumble strips.