The slipform technique of construction allows for the continuous pouring of concrete into walls of a structure and only stops when the full required height of the structure has been reached.
Development of the Slipform Technique
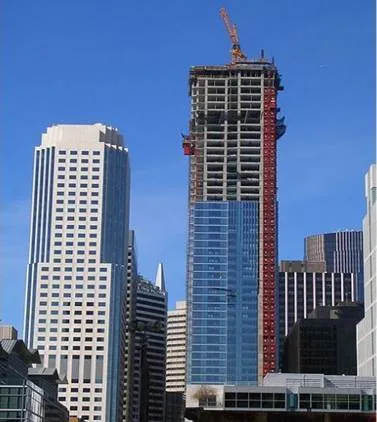
Cement, and concrete by its association with it, has an initial setting time of just about thirty minutes, after which the cement and the concrete have gained sufficient strength to remain in the shape into which it has been poured. It is this property that led to the development of slipform building that allows a non-stop method of construction.
It is this property of early setting that inspired engineers to develop means of moving the formwork so that the concrete can be poured continuously. The height of the formwork is designed in such a way that while the top of the formwork is being filled by concrete the lowest layer of concrete poured earlier has already gained an initial set. When the formwork is moved upwards the concrete that is then exposed remains firm.
Advantages of Slipform Building
A major cost of concrete structure construction comes in the form of the required formwork to retain the concrete while it retains it necessary shape and gains the necessary strength till it can be safely de-shuttered and be able to support itself and other imposed loads. It also requires the formwork to be continually removed to newer locations and then re-erected. All this requires the continuous use of manpower and lifting equipment like cranes. In the case of slipform building, the formwork is erected only once and remains intact until the entire structure is completed.
This greatly reduces the cost of the formwork as well as any time that may be required to erect and move it for re-erection, which can result in huge savings in time as well as money.
The continuous operations also allow for an evening-out of the manpower requirements and also a huge saving in the labor that may have to be periodically employed during otherwise intermittent concreting operations.
The reduction in the movement of formwork and workers also leads to far more safe working conditions that also make it a major advantage.
The Components of Vertical Slipform
A slipform assembly can only start after the foundations of the walls have been correctly laid and a starter for the walls laid out in its correct alignment with all the necessary steel for the walls already in position. The slipform shuttering is then firmly aligned to this starter with the means of yokes on each side of the shuttering that help to keep the panels in position. The yokes are all connected by horizontal crossbeams. Hydraulic jacks are then installed rigidly to the crossbeams that can all act simultaneously so that the entire slipform shuttering moves upwards. The heights of such slipform shuttering will normally be between 1. 1 meters to 1. 5 meters in height. The yokes and horizontal crossbeams are also used to support a working platform that can afford space for men and materials. The jacks climb using jacking rods that are installed within the concrete and become a permanent part of the structure, or can be retrieved if so desired.
The design of the working deck and the yokes and horizontal crossbeams are a very vital part of efficient slipform construction. It is very important that the entire structure be such that its rigidity and shape is maintained at all times. It is quite normal for the two sides of the shuttering to be inclined towards each other at the top with the correct wall dimension available at the center. This allows the shuttering to move easily and eliminates any drag that concrete can cause on the shutters to prevent its free upward movement. The rigidity of the supporting platform is also essential so that all parts of the structure move simultaneously. If there is any lag from one part to the other, this can cause the shuttering to drag and make it difficult to be pulled up. It is also possible to reduce wall thicknesses as the construction gains height and arrangements have to be made in the slipform structure that will enable such reduction at regular intervals.
Non-stop method of Construction
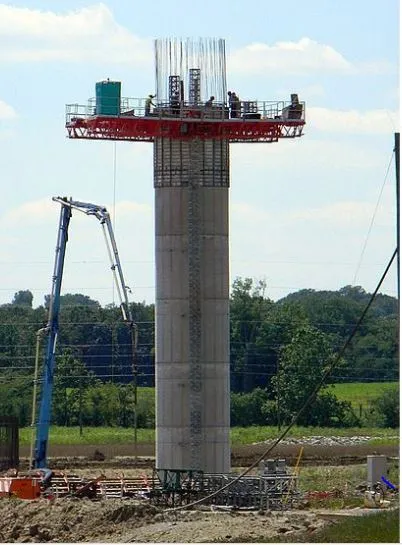
Once the slipform shutters along with the jacks and support deck are in position, concreting operations can then commence. Sufficient working space has to be created on the deck to accommodate reinforcement bar activity. The bars have to be continually lengthened and placed in position as per the structural requirements for the wall. The concrete is poured in layers, and by the time the concrete level has reached the top, the concrete at a level 300 mm above the bottom of the panel should have gained the initial set. The rate of pouring of the concrete has to be adjusted so that this is achieved. The slipform is then moved upwards in steps of 10 mm to 25 mm and both the concreting and placing of the reinforcement bars is done continuously till the final height is reached. All jacks are fitted with brakes that act automatically by mechanical means and do not allow the jacks to slip on the jack rods.
Slipform methods of construction can also be adapted to horizontal structures and are used for paving, canals, and tunneling. The technique is more in use for structures that have continuous walls like silos, chimneys, and piers for very tall bridges. It has also been successfully used for construction of buildings, although this requires the manner of leaving inserts for openings like doors and windows to be decided well in advance, as well as also any necessary inserts to support floor slabs after the walls are constructed.