Glass fiber reinforced concrete is an engineered material that contains cement, polymers, and glass fibers that are ingrained in the cementious matrix. The GFRC properties are influenced by the glass contents, mix design, and production process. GFRC is mainly used for external applications.
Glass fiber reinforced concrete is basically concrete material that utilizes glass fibers for the reinforcement, as a substitute of steel. The glass fibers are normally resistant to alkali. Alkali resistant glass fiber is used extensively since it has a greater resistant to the environmental effects. GFRC is a combination of cement, glass fibers, and polymers. It is normally cast in thin sections. As the fibers are not rusted like steel, protecting concrete coat is not necessary for the prevention of rust. The weight of thin and hollow products produced by GFRC is considerably lesser than the conventional pre-cast concrete. The material characteristics will be influenced by the concrete reinforcement spacing, and the concrete reinforcement mesh.
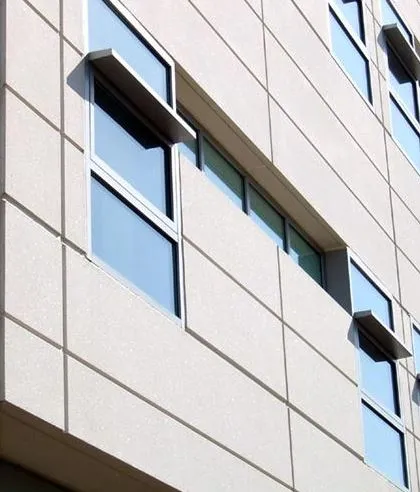
GFRC has developed as a popular material that is used for several applications. There are numerous advantages of using GFRC, as explained below:
GFRC is prepared of minerals and will not easily burn. When exposed to a flame, the concrete functions as a thermal regulator. It protects the materials fixed with it from the flame heat.
These materials are comparatively lighter when compared to the conventional materials. Their installation is therefore fast, and normally simple. Concrete may be produced in thin sections.
GFRC may be cast to almost any shape of columns, wall panels, domes, moldings, and fireplace surrounds.
High strength can be obtained by using GFRC, being tough and resistant to cracking. It has a high ratio of strength-to-weight. Therefore, the GFRC products are durable and light. The transportation costs are reduced significantly being of less weight.
Since GFRC is internally reinforced, other types of reinforcement are not necessary that may be complicated for complicated molds.
Suitable consolidation of mix is achieved for GFRC that is sprayed, without any vibrations. Use of rollers or vibrations, to attain consolidation, is simple for GFRC that is poured.
A good surface finish is obtained, without voids, since it is sprayed and such defects do not appear.
Since the materials have a fiber coating, they are unaffected by the environmental effects, corrosion attacks, and other harmful effects.
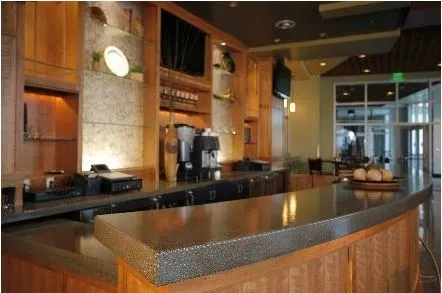
Structural Characteristics of GFRC
Strength of GFRC is developed due to high contents of alkali resistant glass fibers and acrylic polymer. Since the cement contents are high, and the ratio of water to cement is low, the GFRC strength under compressive loads is high. These materials also possess great tensile and flexural strength. The fiber orientation determines the effectiveness of fiber resistance to loads. The fiber must be stiff to ensure the provision of required tensile strength. Thus, the performance of these materials is better than the normal concrete. The high fiber content bears the tensile loads, while the concrete is flexible due to the polymers. The physical properties of GFRC are better than the non-reinforced concrete. Steel reinforcement that has been suitably designed considerably increases the strength of products that are cast with normal concrete or GFRC. However, GFRC cannot substitute reinforced concrete if heavy loads are required to be endured. GFRC are best suitable for light loads. Applications of GFRC are vanity tops, wall panels, and other comparable products. The fiber orientation determines the effectiveness of fiber resistance to loads. The fiber must be stiff to ensure the provision of required tensile strength.
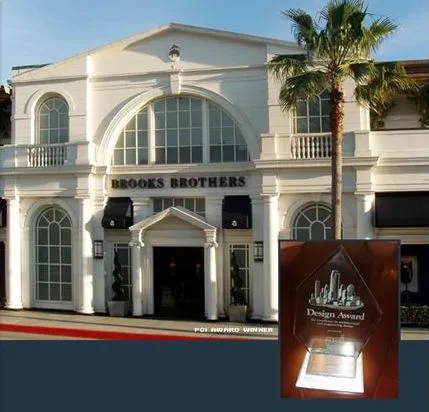
Comments are closed