Marbles are used principally for buildings and monuments, interior decoration, statuary, table tops, and novelties. Colour and appearance are their most important qualities. Resistance to abrasion, which is a function of cohesion between grains as well as the hardness of the component minerals, is important for floor and stair treads. The ability to transmit light is important for statuary marble, which achieves its lustre from light penetrating from about 12.7 to 38 mm (0.5 to 1.5 inches) from where it is reflected at the surfaces of deeper lying crystals. Brecciated, coloured marbles, onyx marble, and verd antique are used principally for interior decoration and for novelties. Statuary marble, the most valuable variety, must be pure white and of uniform grain size. For endurance in exterior use, marble should be uniform and nonporous to prevent the entrance of water that might discolour the stone or cause disintegration by freezing. It also should be free from impurities such as pyrite that might lead to staining or weathering. Calcite marbles that are exposed to atmospheric moisture made acid by its contained carbon dioxide, sulfur dioxide, and other gases maintain a relatively smooth surface during weathering; but dolomite limestone may weather with an irregular, sandy surface from which the dolomite crystals stand out.
The main mineral in marbles is calcite, and this mineral’s variation in hardness, light transmission, and other properties in divers directions has many practical consequences in preparing some marbles. Calcite crystals are doubly refractive—they transmit light in two directions and more light in one direction; slabs prepared for uses in which translucency is significant are therefore cut parallel to that direction. Bending of marble slabs has been attributed to the directional thermal expansion of calcite crystals on heating.
Quarrying
The use of explosives in the quarrying of marble is limited because of the danger of shattering the rock. Instead, channeling machines that utilize chisel-edged steel bars make cuts about 5 cm (2 inches) wide and a few metres deep. Wherever possible, advantage is taken of natural joints already present in the rock, and cuts are made in the direction of easiest splitting, which is a consequence of the parallel elongation of platy or fibrous minerals. The marble blocks outlined by joints and cuts are separated by driving wedges into drill holes. Mill sawing into slabs is done with sets of parallel iron blades that move back and forth and are fed by sand and water. The marble may be machined with lathes and carborundum wheels and is then polished with increasingly finer grades of abrasive. Even with the most careful quarrying and manufacturing methods, at least half of the total output of marble is waste. Some of this material is made into chips for terrazzo flooring and stucco wall finish. In various localities it is put to most of the major uses for which high-calcium limestone is suitable.
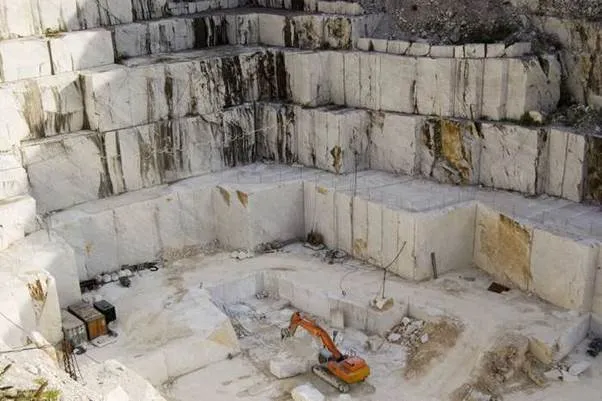
Marble quarry in Tuscany, Italy.