Epoxies are initially in a liquid state that is changed by chemical reaction to a solid state. The basic components in epoxy are hardeners and resins. Due to their excellent properties, epoxy floors, epoxy primer, and epoxy glue are extremely popular.
Epoxy is a thermosetting polymer that is produced from a reaction of a resin with a specific hardener. Epoxy is used as an adhesive in several forms like epoxy primer and epoxy glue. It is used for epoxy floors and other applications. Epoxy thinner is a mix of solvents and alcohols intended for utilization with the majority of epoxy coatings. It is a strong thinner that evaporates rapidly and prevents sags. It has characteristics of corrosion resistant, strong adhesion, and resistance to chemicals. The resin and hardener are mixed in particular quantities to commence curing. When the temperatures at application are high, slow thinners are used to improve the product flow. Rapid evaporating thinners are normally used for spray work to increase atomization, and reduce the probability for sags. These thinners are helpful for roller and brush work at low temperatures since the chances of confinement under the drying paint are reduced.

Epoxies are blended with inert aggregates to attain certain characteristics.
Epoxy has unique characteristics as explained below:
○ Epoxy coatings are widely used due to their exceptional chemical resistance, low porosity, durability, and bond strength.
○ Epoxies contain a curing agent and a base. These elements are blended in a specific ratio. Heat is generated due to a chemical reaction, and the mixture is hardened to produce an inert plastic.
○ Epoxies may lose their shine when exposed to direct sunlight. This yellowing effect is a valid problem that can be resolved by addition of urethanes or latex.
○ Epoxies harden in a short time, but complete curing occurs after several days. After complete hardening is achieved, it is possible to sand the coating. After proper epoxy curing, it can withstand below zero temperatures. High temperatures lower the epoxy viscosity, and also decrease the epoxy application time.
○ Epoxies are by nature brittle and hard. Additives are added that reduce the brittleness, but usually also reduce the chemical resistance.
○ Particular epoxies have been developed with increased resistance to temperatures, chemicals, yellowing, and the ability for underwater application.
○ After mixing of epoxies in a container, these are transferred to another container before application. This process is practiced to ensure proper mixing that may not be adequate if only one container is used. Mixing is normally not satisfactory at the container sides, edges, and corners. This shifting of epoxies from one container to another ensures complete mixing before application.
Epoxies and paints are not recommended to be directly applied to galvanized surfaces. Galvanization is a protecting coat that forms a protective layer. Epoxies that are applied to galvanized surfaces may peel off soon. Galvanized surfaces may be coated only with a superior primer. Similarly, galvanization is not recommended for aluminum surfaces since these surfaces have a tendency to bend, due to which the coating may be removed.
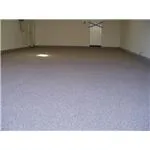
Epoxies have excellent adhesive properties because of the polar bonding, when in contact with different surfaces. On the surfaces that are dry, the epoxy and surface bond dislocates the air. Even underwater, a similar action occurs and the polar bond displaces the water. Therefore, painting undersea is not much different from the painting done above the water. The epoxy’s performance is not much dependent on the environment.
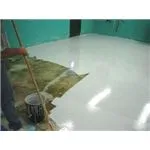
Comments are closed