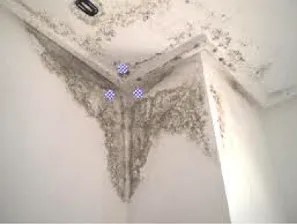
CAUSES OF DAMPNESS
Dampness may be caused by:
(a) Ground water
(b) Rainwater and
(c) Leakages from pipes.
(a) Dampness due to Ground Water: All buildings are founded on soils. Soil holds water for along time. Sometimes water level may rise and come in contact with foundation. Due to capillary action moisture from ground rises into foundation, floor and even in wall.
(b) RainWater: May enter the building components due to various reasons.
(i) From wall top: If top of wall is not protected with impervious course like concrete,
water can enter the wall and keep it damp for a long time.
(ii) From face of external walls: Splashing of outer wall by rain results into moisture entering the wall. Poor plaster coat is the main source of this type of dampness.
(iii) Improper fixing of downtake pipes: If downtake pipes from roof are not properly
fixed, a thin layer of water stagnates near the mouth of downtake pipes. This results into entry of rain water into roof and wall.
(iv) Improper slopes to roof: In flat roofs, many times this is the cause for the dampness of roofs. If slope is not given properly, water ponds are formed on the flat roof, which results into entry of water into slab. Once water enters the slab it remains for long time creating dampness.
(v) Defective construction: Imperfect wall joints, improper slopes to chejja, construction joints in roof etc. cause dampness in buildings.
(c) Leakage from Pipes: From over head tanks, pipes are taken over roof and along the wall. From bathrooms, toilets and kitchen water is drained out with different types of pipes. The pipes are joined to get required length and turns. Many times water leaks through joints resulting into moisture in building components.
ILL-EFFECTS OF DAMPNESS
Ill-effects of dampness are as listed below:
1. Patches develop and destroy the appearance of the building.
2. Colour wash, white wash and paintings are damaged.
3. Plaster crumbles.
4. Bricks and stones disintegrate endangering the building.
5. Steel in the slabs and beam start rusting. It reduces the life of structure.
6. Electric short circuits may takes place.
7. Flooring may settle.
8. Floor covers are damaged.
9. Wooden components of buildings like door frames, cupboard warp.
10. Dry rotting of wood takes place.
11. Termite becomes active and attack wooden articles.
12. Mosquito breeding takes place.
13. Darkness along with warmth and darkness breed germs giving rise to many diseases.
REQUIREMENTS OF AN IDEAL MATERIAL FOR DAMP PROOFING
The requirements of an ideal materials for damp proofing are:
1. It should be impervious.
2. It should be flexible.
3. It should be easy to carry out leak proofing joints.
4. It should be stable.
5. It should be durable. Itβs life should be as much as the life of building itself.
6. It should resist the load safely.
7. It should not contain sulphates, chloride and nitrates.
8. It should be cheap.
MATERIALS FOR DAMP PROOFING
The materials used for damp proofing are:
1. Bitumen: In hot condition it is highly flexible and can be applied with brush to the bedding of concrete or mortar. Thickness of coat provided is about 3 mm.
2. Mastic asphalt: It is a semirigid material. It is obtained by heating asphalt with sand and mineral fillers. It is perfectly impervious. It should be laid very carefully.
3. Bituminous or asphaltic felt: It is a flexible material which is available in rolls. It is provided on roof slabs and parapet walls with an overlap of 100 mm on sides. The laps are sealed with bitumen. They do not withstand heavy movements.
4. Bricks: Good bricks with water absorption less than 5 per cent are sometimes used to make damp proof courses. The bricks are laid in two to four courses in cement mortar.
5. Stones: Stones like granite, trap and slates may be laid over wall to its full width as damp-proof course.
6. Mortar: Cement mortar of proportion 1 : 3 with small quantity of lime and water proofing agents are used to make a water proofing course to foundations, ground floor slabs, top of parapet walls etc. It may be used for plastering external walls.
7. Concrete: To check the rise of water into walls a course of 75 mm to 100 mm cement concrete 1 : 1×1/2 : 3 or 1 : 2 : 4 is provided before starting constructing walls. These courses may be provided with hot bitumen paint as an additional precaution.
8. Metal sheets: Aluminium, copper or lead sheets are provided to seal the construction joints. Over these sheets bituminous seal is provided.
9. Plastic sheets: Plastic sheets are very good course for damp proofing. They are made up of black polythene of thickness 1 mm.
METHODS OF DAMP PROOFING
Various methods of damp proofing are as given below:
1. Providing D.P.C. course
2. Providing cavity walls
3. Surface treatment
4. Integral treatment
5. Guniting and
6. Pressure grouting.
1. Providing damp proof course: It consists of providing a damp proof course between the source of dampness and building component. The DPC may be with any water repellant material like bitumen, mastic asphalt, cementconcrete, metal or plastic sheets. DPC should cover full width of wall. It should be laid on levelled surface of mortar. Joints should be minimum and should not be at critical points. When horizontal DPC on roof is continued on vertical face of parapet wall, the junction should be filled with about 75 mm fillet of cement concrete.
2. Providing cavity wall: Cavity wall may be constructed to protect foundation masonry and the wall The cavity prevents moisture travelling from outer to inner wall.
3. Surface treatment: If moisture is only superficial and not under pressure this method is useful. It consists of application of layer of water repellant compounds on the surface. Some of the water proofing agents used for such treatment are silicates of sodium or potassium and sulphates of aluminium, zinc and magnesium.
4. Integral treatment: It consists in mixing commercially available compounds in water before concrete is wet mixed. These compounds are made from chalk, talc, flutter earth or chemical compounds like calcium chloride, aluminium sulphate, calcium chloride etc. Some compounds contain compounds like soap, petroleum oils, fatty acids etc.
5. Guniting: In this method a mixture of cement and water is forced by cement gun on the surface to be made water proof. Later 1 : 3 or 1 : 4 cement mortar is applied to the surface with pressure using compressed air. Thus an impervious layer of mortar is provided.
6. Pressure grouting: This is the method used to seal cracks in the concrete surfaces. In this method cement grout is forced under pressure.
Comments are closed