PLASTERING
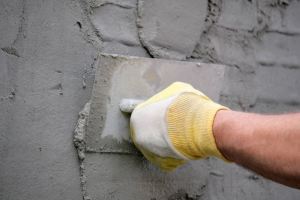
plastering
The following topics are covered in this post.
1. What is plastering?
2. What are the requirements of good plaster?
3. Different types of mortars for plastering
4. Number of coats of plastering
5. How to preparation of background before plastering?
6. What are the recommended mortars mixes for different situation?
7. What are the defects in plastering?
WHAT IS PLASTERING?
Plastering is the process of covering rough surfaces of walls, columns, ceilings and other building components with thin coat of mortars to form a smooth durable surface. The coating of mortar is termed as plaster.
Plastering is done to achieve the following objects:
§ To protect the external surfaces against penetration of rainwater and other atmospheric agencies.
§ To give smooth surface in which dust and dirt cannot lodge.
§ To give decorative effect.
§ To protect surfaces against vermin.
§ To conceal inferior materials or defective workmanship.
REQUIREMENTS OF GOOD PLASTER
The plaster material should fulfill the following requirements:
§ It should adhere to the background, and should remain adhered during all variations in seasons and other atmospheric conditions.
§ It should be hard and durable.
§ It should possess good workability.
§ It should be possible to apply it during all weather conditions.
§ It should be cost efficient.
§ It should effectively check penetration of moisture.
Types Of Mortars For Plastering
The selection of type of plaster depends upon the following factors:
§ Availability of binding materials.
§ Durability requirements.
§ Finishing requirements.
§ Atmospheric conditions and variations in weather.
§ Location of surface (i.e. exposed surface or interior surfaces).
CEMENT MORTAR
Cement mortar is the best mortar for external plastering work since it is practically non-absorbent.
It is also preferred to lime plaster in both rooms etc., and in damp climates. Cement mortar is much stronger than lime mortar. The mix proportion (i.e. cement : sand) may vary from 1:4 to 1:6. Sand used for plastering should be clean, coarse and angular.
Cement plaster is applied either in two coats or in three coats, the former being more common.
For inferior work, single coat plaster is sometimes provided.
NUMBER OF COATS OF PLASTER
The background over which plastering is to be done depend upon the type of wall construction, such as random rubble (R.R.) masonry, coarsed rubble masonry, brick masonry
Note: If plastering is done in single coat only, its thickness should not exceed 12 mm nor should it be less than 6 mm.
TWO COAT PLASTER
The following procedure is adopted:
§ The background is prepared by raking the joint to a depth of 20 mm, cleaning the surface and well-watering it.
§ If the surface to be plastered is very uneven, a preliminary coat is applied to fill up the hollows, before the first coat.
§ The first coat or rendering coat of plaster is applied, the thickness being equal to the specified thickness of plaster less 2 to 3 mm. In order to maintain uniform thickness of plaster, 15 cm x 15 cm size. Two dots are so formed in vertical line, at a distance of about 2 m, and are plumbed by means of a plumb. A number of such vertical screeds are formed at suitable spacing. Cement mortar is then applied on the surface between the successive screeds and the surface is properly finished.
§ Before rendering hardens, it is suitably worked to provide mechanical key for the final or finishing coat. The rendering coat is trowelled hard forcing mortar into joints and over the surface. The rendering coat is kept wet for at least 2 days, and then allowed to dry completely.
§ The thickness of final or finishing coat may vary between 2 and 3 mm. Before applying the final coat, the rendering coat is damped evenly. The final coat is applied with wooden floats to a true even surface and finished with steel trowels. As far as possible, the finishing coat should be applied starting from top towards bottom and completed in one operation to eliminate joining marks.
THREE COAT PLASTER
The procedure for applying three-coat plaster is similar to the two-coat plaster except that an intermediate coat, known as floating coat is applied. The purpose of this coat of plaster is to bring the plaster to an even surface. The thickness of rendering coat, floating coat and finishing are kept 9 to 10 mm, 6 to 9 mm and 2 to 3 mm respectively. The rendering coat is made rough.
The floating coat is applied about 4 to 7 days after applying the first coat. The finishing coat may be applied about 6 hours after the application of floating coat.
SINGLE COAT PLASTER
This is used only in inferior quality work. It is applied similarly as two-coat plaster except that the rendering coat, as applied for two-coat plaster, is finished off immediately after it has sufficiently hardened.
Preparation of background
For plastering new surfaces, all masonry joints should be raked to a depth of 10 mm in brick masonry and 15 mm in stone masonry for providing key to the plaster. All mortar droppings and dust, and laitance (in case of freshly laid concrete) should be removed with the help of stiff wire brush. Any unevenness is levelled before rendering is applied. For finish applied in three coats, local projections should not be more than 10 mm proud of general surface and local depressions should not exceed 20 mm. For two-coat plaster, these limitations are 5 mm and 10 mm respectively. The surface should be washed with clean water and kept damp uniformly to produce optimum suction. In no case should the surface be kept so soaked that it causes the green mortar to slide off, or so dry that it causes strong suction which withdraws moisture from mortar and makes it weak, porous and friable. If plaster is to be applied on old surface, all dirt, oil, paint etc. should be cleaned off. Loose and crumbling plaster layer should be removed to its full thickness and the surface of the background should be exposed and joints properly raked. The surface should be washed and kept damp to obtain optimum suction.
Recommended mortar mixes for different situation
Note: the ratio of lime varies with % purity of lime and these ratios may be suitably adjusted depending upon local practice.
Defects In Plastering
The following defects may arise in plaster work:
1. Blistering of plastered surface
This is the formation of small patches of plaster swelling out beyond the plastered surface, arising out of late slaking of line particles in the plaster.
2. Cracking
Cracking consists of formation of cracks or fissures in the plaster work resulting from the following reasons:
§ Imperfect preparation of background.
§ Structural defects in building.
§ Discontinuity of surface.
§ Movements in the background due to its thermal expansion or rapid drying.
§ Movements in the plaster surface itself, either due to expansion (in case of gypsum plaster) or shrinkage (in case of lime sand plaster).
§ Excessive shrinkage due to application of thick coat.
§ Faulty workmanship
3. Crazing
It is the formation of a series of hair cracks on plastered surface, due to same reasons which cause cracking.
4. Efflorescence
It is the whitish crystalline substance that appears on the surface due to presence of salts in plaster-making materials as well as building materials like bricks, sand, cement etc. and even water. This gives a very bad appearance. It affects the adhesion of paint with wall surface.
Efflorescence can be removed to some extent by dry brushing and washing the surface repeatedly.
5. Flaking
It is the formation of very loose mass of plastered surface, due to poor bond between successive coats.
6. Peeling
It is the complete dislocation of some portion of plastered surface, resulting in the formation of a patch. This also results from imperfect bond.
7. Popping
It is the formation of conical hole in the plastered surface due to presence of some particles, which expand on setting.
8. Rust stains
These are sometimes formed when plaster is applied on metal laths.
9. Uneven surface
This is obtained purely due to poor workmanship.
Comments are closed