Before doing the comparison study let’s know what these terms mean.
CPCC – Cement-Polymer Composite Coated Rebar’s
FBEC – Fusion Bonded Epoxy Coated Rebar’s
CRSD – Corrosion Resistant Steel Deformed Rebar’s
1.0 Corrosion Control of Reinforcement bars (Rebar’s)
40% of failure of structures is on account of corrosion of embedded steel reinforcement in concrete. Therefore corrosion control of steel reinforcement is a subject of paramount importance. First and foremost for corrosion control is the good quality of concrete through good construction practices.
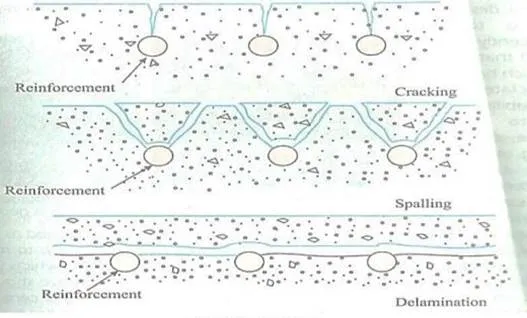

2.0 Cement-Polymer Composite Coated Rebars (CPCC)
System at a glance
Products involved in CPCC normally are:
• De-rusting Solution
• Alkaline Powder
• Phosphating Jelly
• Inhibitor Solution
• Sealing Solution
S No | Parameter | Requirement |
1. | Pre-treatment(Surface reparation) | Sand blasting to the near white metal |
2. | Primer Coat | To be given within 4 hours of sand blasting. |
3. | Sealer Coat | Within 30 minutes of primer coat, this should be given. Thickness 150 microns plus minus 25 microns. |
4. | Air curing | Six hours before use in the work. |
5. | Continuity of coating | No defects such as cracking, bulging, peeling, no rust mark. Inspect visually. |
6. | Adhesion of coating – test | Coated bars are bent at 120 o around a mandrel. NO peeling or cracking should be observed on outer radius. |
7. | Stacking | Stack bars on buffer material. |
8. | Cutting , bending, welding | Coat bars can be cut and bent. Cut ends and weld positions should be treated with same formulation. |
This system has been developed mainly as a factory / shop process.
• The approach behind development of this system is that the base metal of rebars, contains ? electrons which get readily released in corrosive environment leading to oxidation of iron and thereby formation of Ferrous Oxide (II) (rust) as principal deterrent.
• In order to prevent this oxidation a surface coating capable of interacting/nullifying the released electrons is provided.
• Further pre-stressing and reinforcing steel, in concrete during service life, are exposed to an alkaline environment and this necessitates introductions of a top coat which should be compatible to primer and alkaline environment.
3.0 Fusion Bonded Epoxy Coated Rebars (FBEC)
System at a glance
No. | Parameter | Requirement |
1. | Pre-treatment(Surface reparation) | 1. Bars are first cleaned from surface contaminationsuch as oil, grease etc. by chemical process before shot blasting.2. The reinforcement bars are cleaned by shot blasting orgrit blasting to white or near white stage.3. The blast cleaned bars are then heated throughinduction heaters at preset temperature level around 230°C. |
2. | Coating | Hot bars are then fed to the coating booth, where theepoxy powder is sprayed electrostatically. |
3. | Curing and Cooling | Coated bars are then cured and forcedcooled by water spraying to enable handling and testing. |
4. | Continuity of coating | On line and off line holiday checks, thickness checks are carried out. The adhesion of the coated bars is also tested frequently by bending of the bar. |
5. | Testing of Performance ofrebar | Various other tests are performed in laboratory like chemical resistance, short spray, resistance in continuance boiling water, abrasion resistance and impact resistance etc. These are conducted on every batch of production. |
6. | Handling & Stacking | Fusion Bonded Epoxy Coated Bars require padded contacts during transportation, stacking, handling and till the concreting is done. |
7. | Cutting, bending & welding | The cut ends, welded spots and handling damages are required to be repaired with special liquid epoxy compatible with the coating material as per specification of the coating agency. |
• Fusion bonded epoxy is basically 100% solid finely ground fused powder particles, which when heated; melt to form a continuous adherent film.
• There is no passivating primer film provided in case of FBEC rebars.
• This coating introduces a medium of weakness in the path of an intimate bond between rebar and alkaline concrete.
• Extensive investigation carried out on 40 bridges in Florida Key in USA has revealed that disbandment can occur easily in the FBEC rebars which lacked passivation layer of Ferrous oxide (II) and is a precursor to corrosion.
• Higher co-efficient of Thermal Expansion of fusion bonded epoxies impose large thermal stresses in epoxy coating leading to its early failure.
Epoxy coats the rebar in the following manner:
Melts
Flows
Gels
Cures
Cools
Adheres as coating
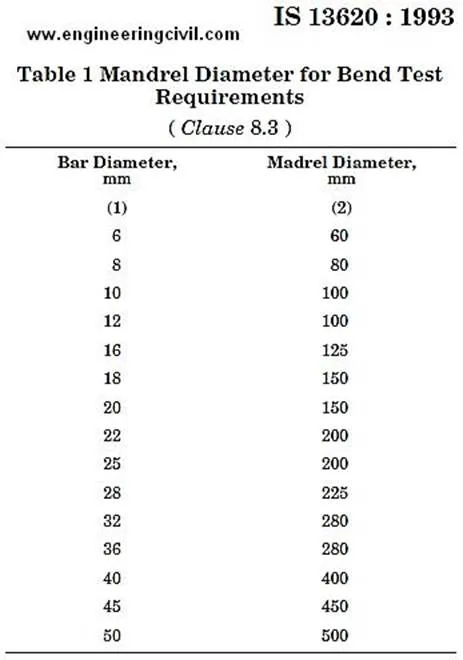
4.0 Corrosion Resistant Steel Deformed Rebars (CRSD)
• Mechanism of resistance to corrosion begins with the formation of initial layer of protective oxide or rust. (Hypo oxides). Unlike common rust on normal rebars, the CRSD rust is passive, tenacious and self-renewing.
• The protective oxide is fine textured, tightly adherent and a barrier to moisture, oxygen, carbon dioxide, Sulphur dioxide and chloride effectively preventing further corrosion.
• Scale on normal bars of steel is coarse textured flaky oxide that does not prevent moisture or oxygen from reaching the underlying bars and continuing the corrosion.
• As corrosion resistance is in the chemistry of the grade, if the passive oxide layer gets removed somehow, a new passive layer is formed immediately.
CRSD – Mechanical Properties | ||
Properties | IS:1786 Fe500D | CRSD |
Yield Stress, YS (min, N/mm2) | 500 | 500 |
% Elongation | 16 | 16 |
Ultimate Tensile Strength, UTS (min, N/mm2) | 565 | 580 |
5.0 Comparison (CPCC – FBEC – CRSD)
Parameters | CPCC | FBEC | CRSD |
Thickness of Coating | 175 mm – 300 mm | 300 mm – 675 mm | No coating required |
Type of Protection to rebar | Extrinsic | Extrinsic | Intrinsic |
Pre-treatment | Pretreatment is required before coating | Pretreatment is required before coating | No pre-treatment required |
Treatment to surface | Before coating the surface made little rough when some damage is introduced. | Before coating the surface made little rough when some damage is introduced. | The surface of the finished good is not disturbed or damaged at all. |
Temperature treatment | The whole process is done at room temperature. | 230°C – 400°C | No treatment required |
Special Bending requirement | Modified mandrel diameter is specified by Indian Standard | Modified mandrel diameter is specified by Indian Standard | Same as other TMTrebars of Fe 500D grade |
Defects introduced | Holiday Effect | Holliday Effect | Nil |
Comments are closed