Membrane filtration is considered very efficient and is often used in addition to slow sand filtration and other methods to ensure the quality of drinking water.
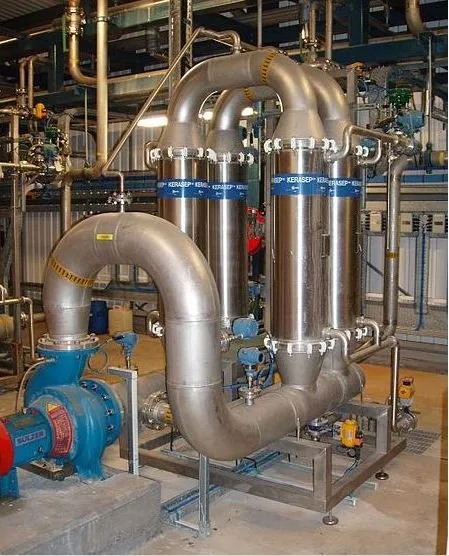
A filter is a porous barrier that allows water to pass through it. The efficiency of a filter depends on the size of the pores, which in turn is determined by the size of the impurities that need to be removed. Very fine impurities that are quite often in colloidal form will not be removed by these filters, however small the pore size. This is where semi-permeable membranes, which have pore sizes measured in angstrom units, are used. There are different types of membranes in use for membrane filtration, and each one requires different operating pressures. The most efficient type of membrane uses the reverse osmosis principle to filter impurities.
The application of membrane filtration for drinking water is now considered the standard for most filtration plants. The cost of membrane filtration is dependent on the usage of power required to force the raw water though the membranes or the creation of vacuum to assists the same process. Recent developments in membrane research have led to low pressure membrane technology. The efficiency of membranes in the filtration of water is largely dependent on the maintenance of the membranes, and this has led to standard operating procedures for membrane filtration that allow the filtration plant to work at maximum efficiency at all times, both in terms of purity of the drinking water, and the lower use of inputs that add to the cost.
Operating Modes of a Membrane Filtration Plant
The operations of a membrane filtration plant are divided into a number of modes.
The service time is when the filtration process is in progress and the membranes are generating the necessary filtrate water, and a plant is considered efficient if it is in service for about ninety eight percent of the working day. The standard operating procedure during the service mode requires constant readings of the filtrate turbidity, measurement of the filtered water quantities through flow measurement, pressures on the membrane, and pump parameters. Most of these are obtained through automatic control, and the operator needs to constantly monitor the readings to ensure maximum efficiencies as per set standards. Deviations have to be brought to the attention of operations staff.
Membranes do get fouled with particles that are too big to pass through them and tend to clog up the membrane and increase the pressures needed for efficient filtration. SOP for membrane filtration plants require that such fouling is removed by backwashing or cleaning in place. Back washing quite often uses a combination of air and water with water and air pumped in the reverse direction to clear the membrane. The frequency of such backwashing will depend on the quality of the raw water and is something that will have to be determined by analysis of the raw water and subsequent instructions to operators. The entire process interrupts the flow of filtrate for just about 60 seconds, and this frequency can be often be adjusted to a little as two or three times an hour.
Chemicals are sometimes used to assist the cleaning, and the same pumps that govern the flow of the filtrate can be used with switching of valves. In-place cleaning of membranes using chemicals is also done at regular intervals.
Standard practices for membrane filtration require the replacement of membranes at regular intervals as suggested by the manufacturers of the membranes. The ease of making these changes quite often governs the type and fitment of the membrane filtration unit. These may also have to be tests carried out